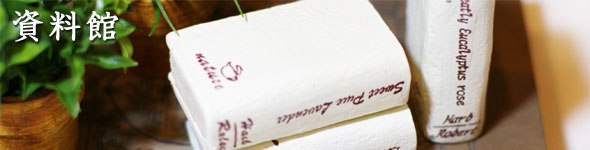
加工技術(鍛造)
金属材料(炭素鋼・ステンレス鋼・合金鋼・非鉄金属)を金型を用いて圧縮成形(弾性限界を超える外的な力を与え、永久ひずみを起こして望む形状や寸法に加工)するのが鍛造です。 加工を受けた製品は、組織の微細化し、耐摩耗性がよくなります。金属繊維(ファイバーフロー)が断ち切れていないことや、加工硬化による強度上昇によって、軟質材の場合には被削性向上などの利点があり、兼価な素材の使用や、熱処理の省略ができる場合もあります。 |
![]() |
この加工法の優れている点は、1分間に数個〜数百個と言う高い能率で、素材から最終形状またはそれに近い状態にまで加工できるところです。また、成形精度が高く、後工程での加工が少なくなります。 鍛造を温度別に大別すると「熱間鍛造」・「冷間鍛造」・「温間鍛造」の3っに分かれます。また、鍛造はいろいろな変形様式を含み、その中に端面矯正・前方押出し加工・後方押出し加工・据え込み加工(アプセット)・穴抜き加工(ピアシング)・打ち抜き加工(トリミング)等があります。 |
冷間鍛造 【COLD FORGING】
常温(室温)下で金型工具を用いて、金属材料(炭素鋼・ステンレス鋼・合金鋼・非鉄金属)に弾性限界を超える外的な力を与え、永久ひずみを起こして望む形状や寸法に加工(圧縮成形)する工法です。 |
![]() |
温間鍛造 【WARM FORGING】
材料を200〜850℃まで加熱し、材料の変形抵抗を減少させて、靭性をいくらか犠牲にしても材料の強度を確保し、金型工具を用いて、金属材料(特に、高炭素鋼やSUS304など難成形材など)に弾性限界を超える外的な力を与え、永久ひずみを起こして望む形状や寸法に加工(圧縮成形)する工法です。「熱簡鍛造」と「冷間鍛造」の中間領域にある新しい鍛造法です。 |
熱間鍛造 【HOT FORGING】
材料の再結晶温度以上の鍛造加工を「熱間鍛造」といいます。再結晶温度は純鉄は630℃、鋼材900℃ですが、熱間鍛造の場合は一般には1100〜1250℃を言います。「熱間鍛造」は加工後に再結晶して軟化するため可鍛性が失われないという特色があります。 | ![]() |
フォーマー(横型多段式鍛造機)での鍛造方法
圧造用のコイル材を矯正機にて直線に矯正し、送り機構部の送りロールにてコイル材を切断機構部まで供給します。供給されたコイル材料をナイフ・クイルにて一定寸法の長さ(切断長さは材料ストッパーの位置で調整)で切断します。切断されたワーク材は、複数の圧造工程内に搬送機構部(トランスファー・チャック爪)にて搬送し、搬送された各圧造工程内では金型と金型でワーク材を圧縮成形し、連続的に目的の形状の製品を成形します。 | ![]() |
圧縮成形方法(圧造加工方法)
端面矯正・前方押出し加工・後方押出し加工・据え込み加工・穴抜き加工・打ち抜き加工(トリミング)等があります。 |
切断
送り機構部の送りロールによって切断機構部まで送り込まれたコイル材は、ストッパーの位置で一定寸法の長さに調節され、ナイフとクイルによって右図のように切断されます。材料の機械的性質によって、ナイフとクイルのクリアランス(隙間)を調整したり、クイルの端面形状を変更する必要があります。 切断面の種類の中には、圧造品(製品)の形状、外観に影響を与える場合があるため、重要な工程になります。 |
![]() |
端面矯正
切断時のワーク材の両端面には凸凹・傾き・歪み等があり、側面側も切断ナイフによる圧痕(圧こん)が発生するため、端面矯正を行う事で両端面側の形状を揃えることにより、次工程での成形条件を良くする効果があります。 この工程は、圧造品(製品)の寸法・形状に大きな影響を与える場合があるため、重要な工程になります。 |
![]() |
前方押出し加工(カップ成型)
金型内(ダイス)にワーク材を密閉または半密閉した状態にし、加圧するパンチの加圧方向(進行方向)と同じ方向にワーク材を流動させて、ダイスとカウンターパンチの隙間を通してワーク材の断面積の減少をはかる方法で、円筒状の製品をつくるのが目的です。 | ![]() |
前方押出し加工(軸絞り成型)
金型内(ダイス)にワーク材を密閉または半密閉した状態にし、加圧するパンチの加圧方向(進行方向)と同じ方向にワーク材を流動させて、ダイスの成形部を通してワーク材の断面積の減少をはかる方法で、段付軸の製品をつくるのが目的です。 | ![]() |
後方押出し加工(カップ成型)
金型内(ダイス・パンチ)にダイに隙間なく嵌合(かんごう)するワーク材を密閉または半密閉した状態で圧縮し、加圧するパンチの加工方向(進行方向)とは反対向きにワーク材を流動させて、パンチとパンチ側ピンとの隙間に通して、ワーク材の断面積を減少させる方法で、円筒状の製品をつくるのが目的です。 | ![]() |
後方押出し加工(軸絞り成型)
金型内(ダイス・パンチ)にダイに隙間なく嵌合(かんごう)するワーク材を密閉または半密閉した状態で圧縮し、加圧するパンチの加工方向(進行方向)とは反対向きにワーク材を流動させて、パンチの成形部を通してワーク材の断面積を減少させる方法で、段付軸の製品をつくるのが目的です。 | ![]() |
据え込み加工
ワーク材の軸部方向に圧縮して、直径方向に広げる加工方法です。ワーク材の端部・中間部・全体を膨らませる場合があります。据込加工には、自由据込、半密閉据込、密閉据込があります。![]() ブランクを平行な工具の間で圧縮する単純据込や、片側または両側の一部をパンチやダイで拘束して残部を据え込む方法です。据込によって直径が増した部分は、工具との摩擦によって太鼓形となり、ワーク材の表面の欠陥が拡大されて現れることがあります。 ![]() パンチやダイス、またはその両方によって据込まれた部分を更に拘束して、余分の材料をパンチとダイスの間でバリとしてはみ出させる方法です。成形に必要な圧縮荷重は自由据込に比べ、はるかに大きくなりますが、製品の欠陥が少なくなります。 ![]() ワーク材は、ダスイの内部に完全に密閉されて据込まれるので、鋭い角部や段付、面取り部などが充分に成形できる方法です。ただし、成形荷重は据込方法の中でもっとも大きく、ワーク材の体積を正確に揃えないと金型を破損させる危険性があります。 |
![]() |
穴抜き加工
ワーク材の内径部をパンチまたはダイス側ピンで貫通させ、製品に所要の穴をあける加工方法です。 | ![]() |
トリミング加工
ワーク材の一部外径側を機械のトリミング機構を利用し、円筒形に加工したボルトなどの頭部をトリミングパンチで四角や六角、あるいはギヤー形状に打ち抜いたり、縁取りをする加工方法です。 | ![]() |